Micronova – a sustainable multi-user semiconductor R&D piloting environment

VTT and Aalto University operate a sustainable multi-user semiconductor R&D cleanroom in the Micronova facilities in Espoo, Finland. The cleanroom is part of OtaNano, Finland’s national research infrastructure for micro-, nano- and quantum technologies. More than twenty external companies use the open access cleanroom facilities daily for their own R&D and piloting activities, making it a sustainable manufacturing option.
Key facts
The sustainable multi-user semiconductor piloting environment in Micronova supports the processing of different technologies including MEMS and MOEMS, superconducting quantum devices, RF components, integrated photonics devices, 2D materials and post-CMOS processed components, radiation detectors, thin film components, 3D integrated modules, wafer level packaging and back-end processes.
More than 20 external companies use the 2,600m2 large open access cleanroom daily for their own R&D and piloting needs with their own personnel.
We offer the entire development cycle of micro-, nano- and quantum technology devices from material, device and process innovation to prototyping and small-scale manufacturing.

Our services are tailored to your needs
We offer research and development services of new materials, technologies, devices, systems and processes. We also offer access to our cleanroom and process equipment. We are unique as you get the entire development cycle from fundamental research and process development to prototyping and small-scale manufacturing under the same roof. By partnering with VTT, you benefit from our environmental expertise and actions.
- Research and development services
- Application-specific novel material modelling, development and manufacturing
- Device and process design and innovation
- Prototyping and piloting, small-scale manufacturing
- Access to cleanroom facilities
Environmental actions a priority for over a decade
The Micronova cleanroom complex covers an area of 2,600m2, making it the largest R&D cleanroom in the Nordics. VTT has focused on reducing the footprint of the cleanroom for more than a decade. We have been able to reduce the process equipment energy consumption per usage hour by more than 40% from 2013 to 2022 through more efficient use of our processing equipment. We closely follow indicators for our water, energy and chemical consumption and efficiency, as well as for the hazardous waste that we create, to minimise our footprint. We also increased the neutralisation capacities of acids and bases to reduce the amount of hazardous waste delivered to our waste management company.
Micronova cleanroom facilities

Meet our experts


Cleanroom characteristics
- Total Area 2,600m2
- Cleanroom Classification ISO 4…ISO 6
- Temperature 21 °C ± 0,5 °C
- Relative humidity 45% ± 5
- Clean bay – Service chase type
- Raised perforated floor
- Subfab with technical support areas
Our Micronova cleanroom holds the ISO 9001:2015 certification for research and development work and pilot manufacturing for devices for micro-, nano-, photonics and quantum technology applications, wafer processing services and facility maintenance.
Cleanroom is run by dedicated maintenance, process engineering, quality and cleanroom operations professionals.

World-class infrastructure for R&D and small-scale manufacturing
In Micronova, we also have multiple laboratories suitable for a variety of R&D needs, including:
- Laboratories for characterisation, system-level demonstration, space qualification (such as Millilab, ESA’s external laboratory for millimeter wave technologies)
- Laboratories for quantum and cryogenic characterisation, optics and photonics characterisation
- A sensor laboratory equipped to meet all electronics development needs
Processing capabilities in Micronova fab: VTT has 200+ pieces of equipment in the semiconductor fab
Lithography
- i-line stepper, 5:1, 0.35 µm CD
- Contact/proximity aligners
- Electron-beam writing
- Automatic CD and defect measurements
Etching
- Plasma etching of Si, SiO2, Si3N4, Al, Mo, TiW, Nb + more
- Anhydrous HF vapor etching for SiO2
- Wet etching, variousXeF2 etching
Deposition
- Seven sputtering tools for various metals and piezoelectric materials
- LPCVD of silicon nitride, polysilicon, and silicon dioxide
- PECVD; silicon nitride and silicondioxide
- ALD: aluminium oxide, titanium oxide
Plating, Spin Coating
- Cu (via or wiring), Ni, Sn-Ag, Sn-Pb, In-Sn, AuPolyimide
3D Integration
- CMP of Si/SiO2 or copper
- Direct wafer bonding
- Thermocompression bonding for wafer level packaging
- Wafer grinding
- Spin-etching
- Thin-wafer handling
- Ion trimming
Characterization
- Scanning electron microscope
- Scanning probe microscope
- Scanning acoustic microscope
- Optical film characterisation
- Profilometers
- Atomic force microscope
- Alignment accuracy measurement
Back End
- Wafer dicing
- Flip-chip bonding
- Wire bonding
Ion Implantation
- Medium-current; n- or p-type doping of silicon
Testing
- Wafer level test systems
- High speed electrical and optical testing capabilities
- Multiple labs for offline testing and characterisation
Our cleanroom in 360° view
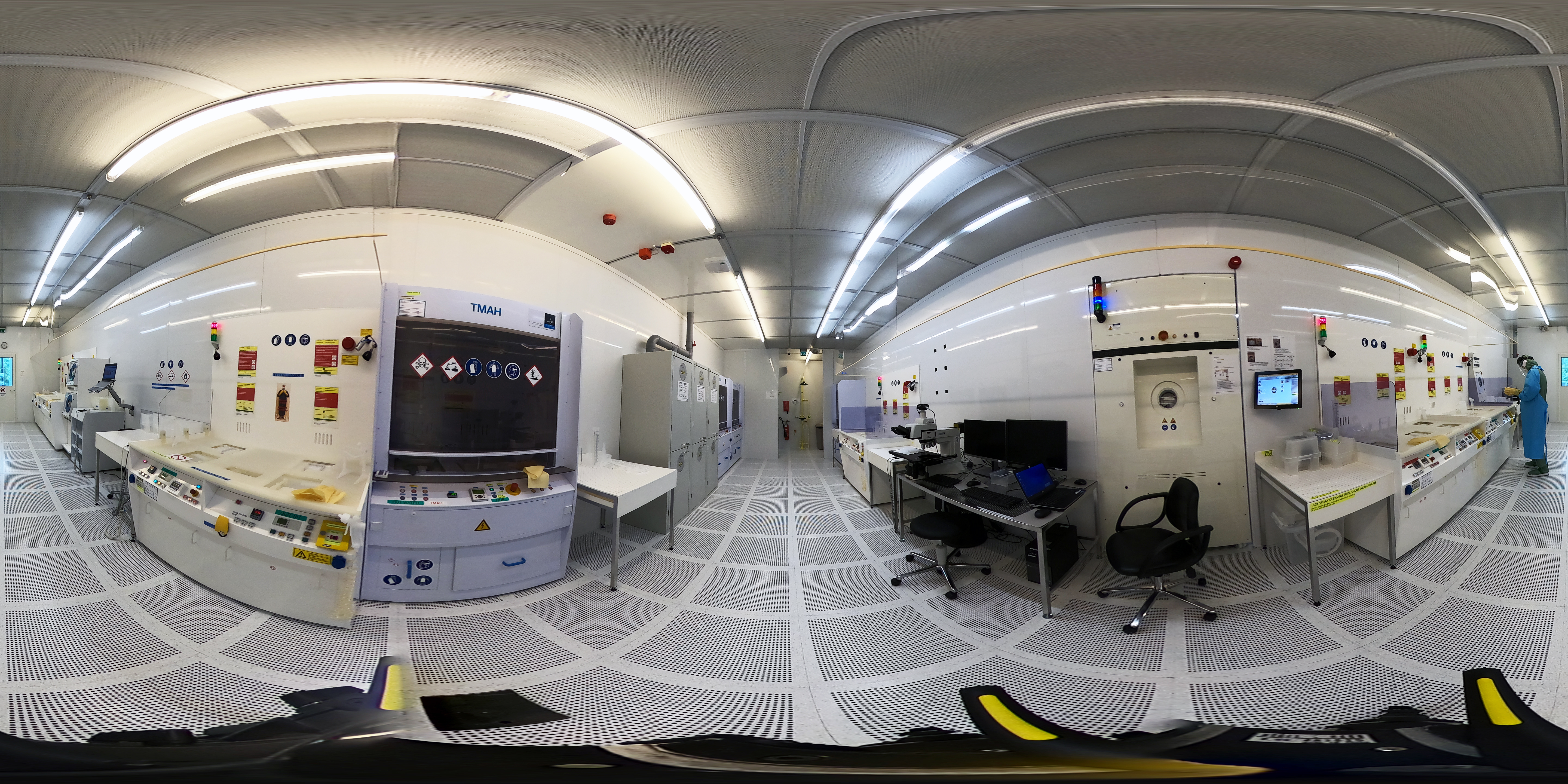
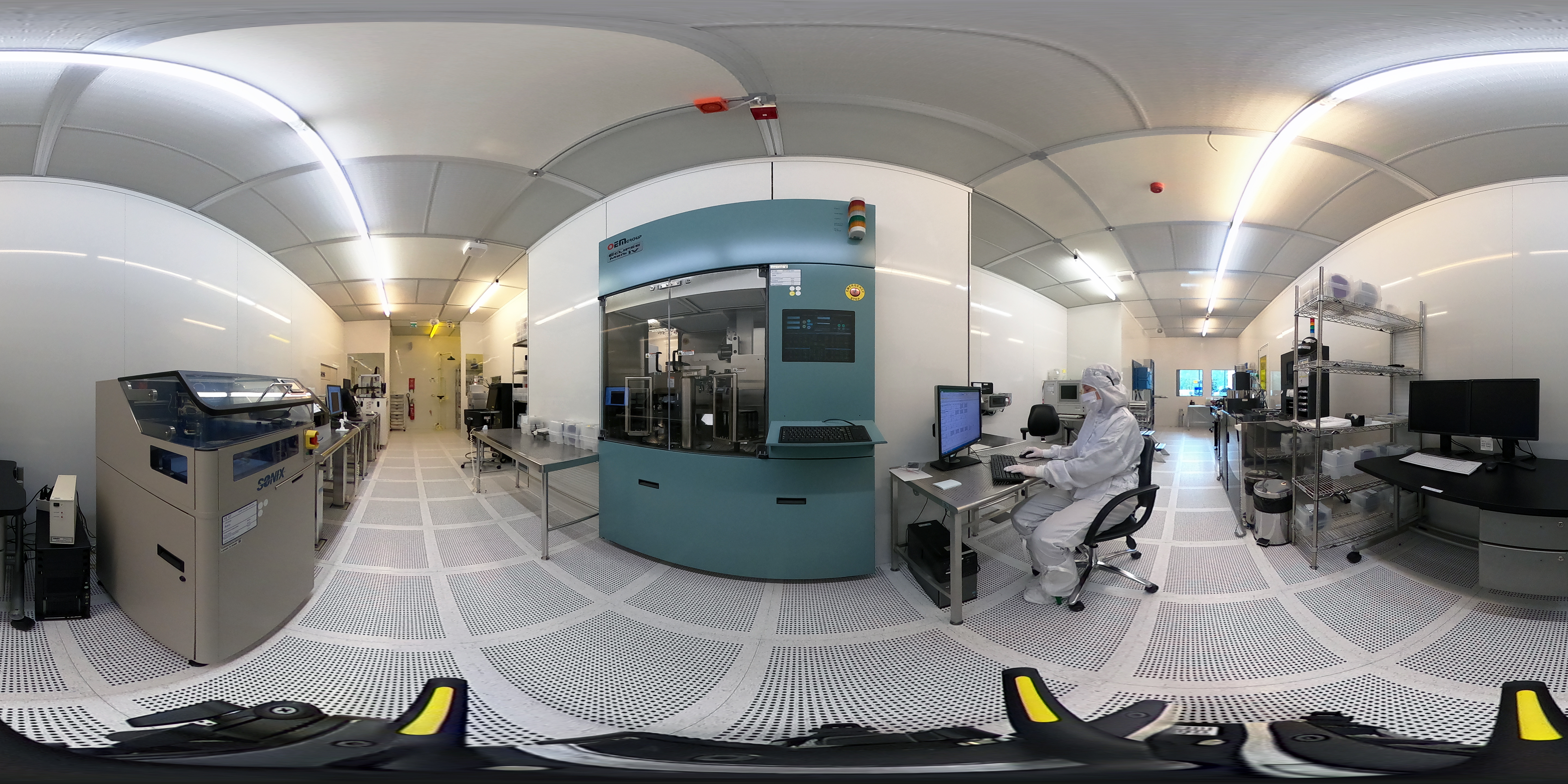
Related infrastructure
Otaniemi – An expanding hub for the Finnish microelectronics ecosystem
The open access cleanroom facilities make Micronova a central hub for the Finnish microelectronics industry ecosystem. Instead of investing in their own infrastructure, companies can use Micronova’s facilities for their own R&D needs. This brings companies together organically and facilitates the planning of joint projects and efforts.
A joint innovation hub for companies and research operators, Kvanttinova, will be built in Espoo and complement Micronova’s already extensive processing capabilities. Kvanttinova is a joint initiative of VTT, Aalto University, the City of Espoo, the Technology Industries of Finland's semiconductor industry group and other companies, to build a new joint RDI cluster and cleanroom environment for microelectronics and quantum technology.