Foam forming platform
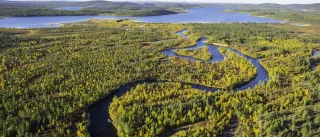
The paper and board industries are undergoing a big shift. Demand for traditional paper products decreases while demand for sustainable plastic alternatives increases. In this scenario, foam forming technology can be used to produce new, value-adding and high-performing structures.
Key facts about foam forming
Foam forming technology widens the product portfolio of the forest industry.
New, sustainable products can be produced with small changes to current production lines.
At VTT, we have been creating and piloting unique foam forming solutions for over 15 years.
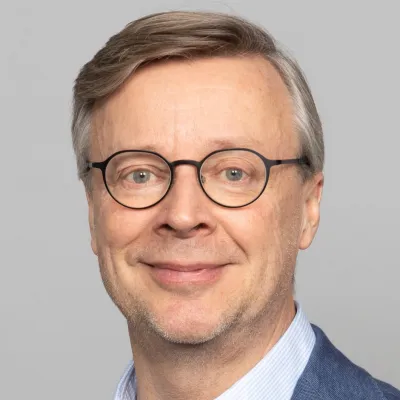
New opportunities and improved sustainability with foam forming
Recyclability and biodegradability are vital properties in today’s materials in packaging, construction, and many other sectors. This provides great opportunities for the forest industry to widen its product portfolio by providing sustainable, bio-based materials produced with foam forming technology.
Current paper and board manufacturing processes have some major limitations: they use a lot of water and energy and have limited capability to handle different raw materials. Products made with the current technology are always quite dense and paper-like.
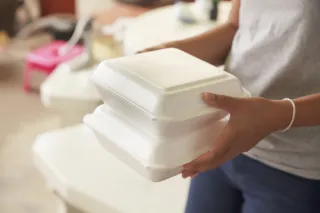
One of the most potential technologies beyond paper and board manufacturing is foam forming technology, where water is replaced with aqueous foam.
Foam forming can be used to produce unique structures using bio-based materials. The resulting products can be further converted for various uses such as packaging, filters, or hygiene products.
These materials are sustainable alternatives to fossil-based packaging materials and nonwoven fabrics. They are highly recyclable, and less energy and water are needed to make them. This helps companies meet sustainability targets and delight consumers with eco-friendly options.
Forerunners in foam forming technology
Our foam forming pilots have resulted in unique solutions used by groundbreaking new businesses. As an example, Paptic, a spin-off company from VTT, produces sustainable packaging materials that have been embraced by brands and consumers around the world.
At VTT, we have been developing foam forming technologies for over 15 years. Our expertise forms the backbone of each project, but every pilot in our state-of-the-art facilities is tailored to the needs of the customer. The resulting intellectual property is owned by the customer: your solution is unique.
We can help you optimise raw materials, processes, and product properties. With the support of our experts and customised production processes, you’ll be able to expedite the upscaling of production.
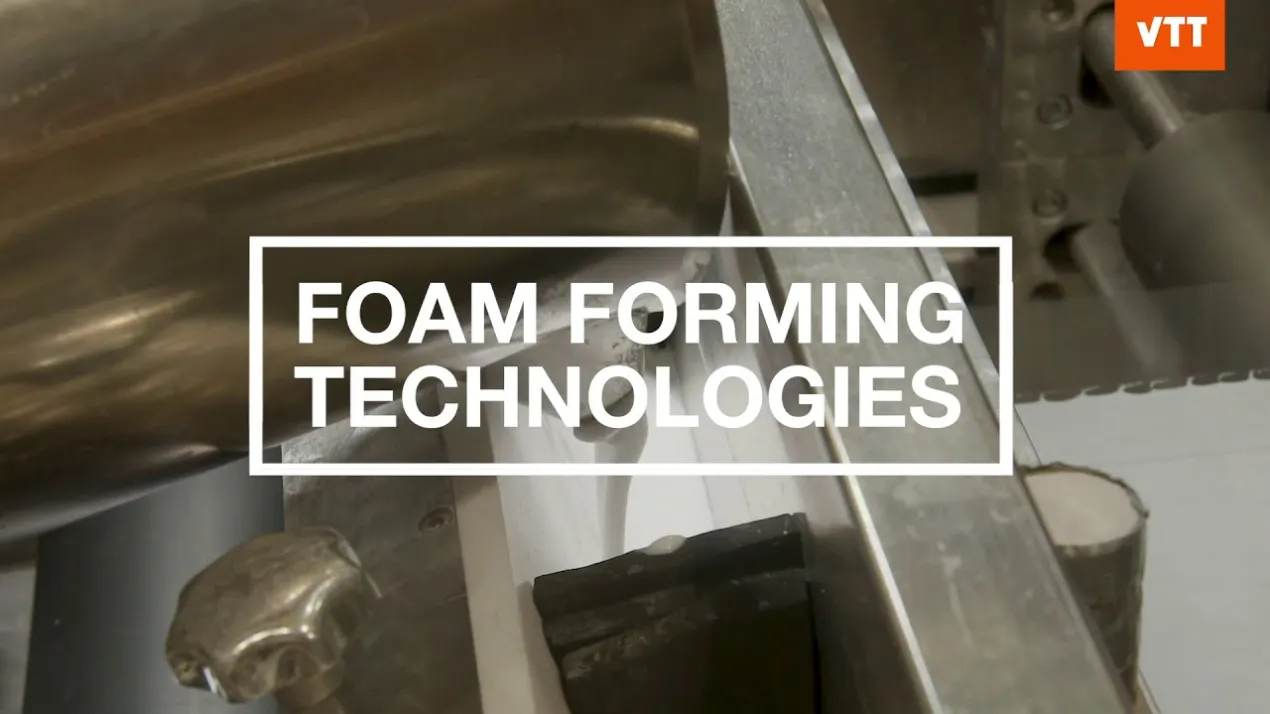
Solutions and questions foam forming can help with
Here are some questions we have helped our customers with:
- Can I use my existing paper machine to produce nonwoven filters or wipes?
- How can I replace plastic with a recyclable material using foam forming?
- How could I improve my product by switching the production process to foam forming?
- How could my business benefit from using foam forming?
How to work with us
When it comes to foam forming technology, there are many ways to utilise our expertise.
-
Contact us!
Tell us what you want to do, and we will figure out how to do it. No project is too small or too ambitious – we would love to hear from you. After the initial assessment, we might be able to offer some of these options. -
Customised partnership
Every research case is unique, and we’re happy to tailor our services to your needs. You will get full ownership of the intellectual property rights of any project we undertake together. -
Cooperative project
We frequently participate in research and development projects with multiple business partners and funding agencies. In cooperative projects the risk is split between multiple organisations and everyone benefits from the results. -
Our networks at your disposal
We are happy to put you in touch with the ideal sparring and development partner.
Contact us here!
Experts at foam forming
We have been creating unique foam forming solutions for over 15 years. Meet our experts!
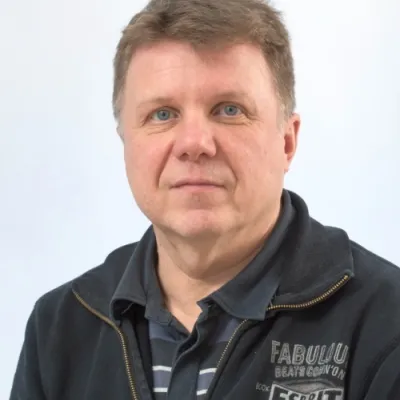
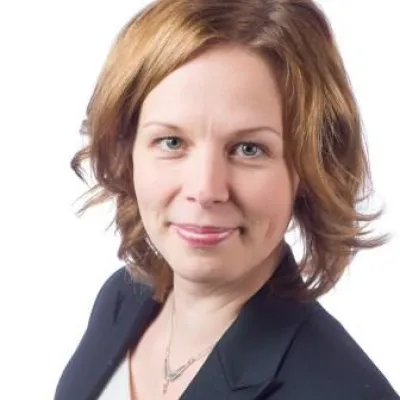