Additive manufacturing offers design freedom, improved life-cycle planning, and cost savings, among other things. That's why VTT is hard at work developing 3D printing technologies and new materials. Over the past eight years, the research centre has produced more than 500 prints of 50 different alloys. And that is just the beginning.
Additive manufacturing (AM), more commonly known as 3D printing, is set to revolutionise industrial production methods. It allows greater freedom of design and no longer restricts the design of parts in the same way as traditional manufacturing methods. As a result, many of today's equipment and components can be reimagined in entirely new ways.
Additive manufacturing also delivers cost savings. The technology allows for lighter structures, which directly affect the cost of items such as satellites or aircraft. Since a lighter aircraft built from lighter components consumes less fuel, significant fuel savings can be achieved over the lifetime of the aircraft. Similarly, if the weight of a satellite is reduced by, for instance, one kilogram, its price can be up to 10 000 euros cheaper.
VTT is a pioneer in additive manufacturing and has invested in the development of 3D printing technology and new alloys for the past ten years.
Over 500 prints, 100 alloy changes and 50 different alloys
In the approximately eight years it has been in operation, VTT's SLM Solutions SLM125HL metal printer has already produced more than 500 prints. This remarkable figure is the result of an experienced team of ten people dedicated to 3D printing as well as a full-time operator.
Having a large, multidisciplinary organisation has also helped: the research centre is constantly involved in a multitude of research projects that provide work for the printer
"When you have many teams working together, you never run out of ideas. New ideas keep coming from new directions," says Tuomas Pinomaa, Customer Account Lead at VTT.
While production printers typically only print on one or two materials, the range of materials at VTT is exceptionally wide: we have produced prints from anything from magnetic materials to titanium and high-entropy alloy (HEA) materials.
The metal powders produced at VTT are tailor-made.
We can do just about any powder in-house. We have expertise ranging from computational design of materials to testing under one roof.
"We strive to go beyond the obvious with every run we do. We don't want to print something obvious or commonplace, but always aim for something new and value-adding," says Pinomaa.
"There are very few things we would say no to. Usually, we want to give everything a try," he continues. "And even though we have already tried many things, we want to keep learning."
Rethinking the electric motor
One of the things made possible by VTT's open and innovative work culture is a critical examination of the electric motor.
The electric motor is more than a 120-year-old invention that has been fine-tuned over the years. However, additive manufacturing and the design freedom it allows are also opening up new development paths for electric motor designers. Which is why VTT challenged itself to rethink the motor in a completely new way.
"We set out to disassemble the motor and to think outside the box as to what we could print," says Pasi Puukko, VTT's Senior Scientist. "We decided to focus on the most difficult part of the engine: the active components, the stator and the rotor. Our aim was, among other things, to reduce critical ground metals and to tackle the losses generated in the engine through design."
VTT's multidisciplinary approach served as an asset in this project too, as there are experts capable of modelling machinery, manufacturing any kind of alloy, and printing any shape under the same roof.
Now, a third version of the demo motor is in the pipeline, with further improvements to the mass-to-power ratio.
Not everything should be printed
Although additive manufacturing allows for new forms and development paths, it is also a complex manufacturing method. Therefore, not everything should be printed.
"3D printing should be purpose driven. Before doing anything, it's important to think critically about what should be printed and where the greatest benefit lies," says Puukko.
To make the deliberation easier, VTT has put together a set of useful questions. They are designed to help clarify whether additive manufacturing could be useful in different situations. The questions include:
- Could the part be lighter?
- Could the lifetime of the component be increase?
- Could several parts be replaced by an assembly?
"If the answer to any of these questions is yes, then 3D printing might be a viable solution," says Pinomaa.
Want to find out more? Get in touch!
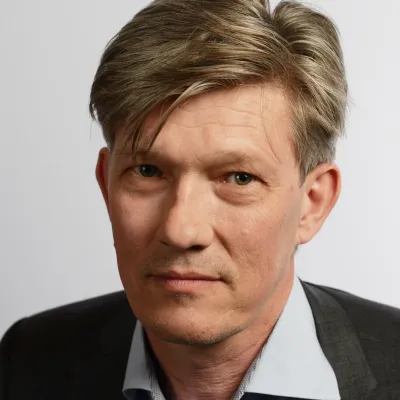