As demand for carbon-neutral processes grows, hydrogen is set to replace fossil fuels in many industrial activities. When paired with the right materials, hydrogen is safe to handle and can be transformed into high value-added products that contribute to combating climate change.
The production of emission-free hydrogen will increase significantly in the coming years. In Finland, the government has set an ambitious goal of becoming Europe’s leader in the hydrogen economy and producing at least 10% of the EU’s green hydrogen by 2030.
As more green hydrogen enters the market, refining it into products with higher added value becomes ever more lucrative. And as fossil fuel prices surge, new hydrogen-based processes are becoming increasingly competitive.
To transition to hydrogen-based production safely and effectively, new and existing processes must be converted to operate with hydrogen. A deep understanding of materials and their performance is required to achieve that.
Hydrogen is set to transform old processes and create new ones
So, what will we do with all that emission-free hydrogen?
Many of the present-day processes used by the chemical industry depend on crude oil and natural gas. Hydrogen makes it possible to replace these fossil fuels and raw materials with a carbon-neutral alternative. For example, the oil and natural gas used by the chemical industry can be replaced with hydrogen and carbon monoxide as a carbon source. Introducing green hydrogen into the Fischer–Tropsch synthesis (FTS), for example, allows us to produce methane, methanol, ethanol and many other base chemicals used by the chemical industry. When carbon dioxide is captured from the atmosphere or combustion processes and transformed into carbon monoxide via the water-gas shift reaction, the Fischer–Tropsch synthesis can also produce carbon-neutral fuels, so-called e-fuels, such as synthetic gasoline, diesel, and kerosene.
Another well-known process that can be made carbon-neutral with the help of green hydrogen is the Haber–Bosch process. This Nobel Prize-winning process is more than a hundred years old and the primary industrial method of producing ammonia. For instance, the green ammonia produced with emission-free hydrogen can be used for fertiliser production or as fuel for ships.
When used as a fuel, hydrogen gas can be burned directly, for instance, in combustion engines that run on hydrogen instead of fossil fuels. The application has a great potential for long-range transportation with ships and planes. Fuel cells, like the polymer electrolyte membrane (PEM) fuel cells, have a higher efficiency than combustion engines and are more suitable for powering cars and trucks.
In addition to replacing fossil fuels in existing applications, hydrogen enables new use cases. For example, the carbon used by the steel industry to reduce iron ore in blast furnaces can be replaced by hydrogen gas to produce direct reduced iron (DRI) – a valuable raw material for steelmaking.

Compatible materials ensure the safe use of hydrogen
Hydrogen is a highly flammable and explosive gas that must be handled correctly. Due to its small molecule size, hydrogen often diffuses relatively fast through materials and small leaks. Interaction with metals can lead to embrittlement and blistering, and with polymers to swelling, cracks or foaming. The lack of proper safety controls can result in catastrophic events, such as the Hindenburg airship disaster in the 1930s or the Challenger explosion some 50 years later. While many of us still recall the images of these events, such large accidents with hydrogen are actually very rare. When handled correctly and paired with compatible materials, hydrogen is a safe gas to use.
There are many stages in a process when engineering materials may come into contact with hydrogen. First, hydrogen needs to be supplied to and perhaps also stored at the facility using hydrogen. Then, the gas needs to be distributed inside the plant to the process stages where it is needed before it is finally used in the process. The storage and distribution of hydrogen often takes place at ambient and sometimes even cryogenic temperatures or elevated pressure. These conditions demand different material properties than process environments where increased temperatures and pressure are not uncommon. Appropriate material selection is a demanding task as both the influence of hydrogen on the engineering material and the effects of temperature and other chemical compounds used in the process must be considered.
Before introducing hydrogen into existing processes, it’s crucial to study all the materials that will be in contact with the gas. If a material is found to be incompatible with hydrogen, the part must be changed. For instance, the burners used for residential heating or in industrial applications must be adjusted to the new fuel. If this is not possible, they must be upgraded as hydrogen has different combustion properties than the commonly used natural gas and propane.
Pairing LNG, ammonia, and hydrogen with the right materials
Natural gas, ammonia and hydrogen are all gases that can be stored as a liquid at low temperatures near ambient pressure. While liquefied ammonia boils at -33 °C, the boiling point for liquified natural gas (LNG) is -162 °C and for hydrogen (LH2) -253 °C.
The idea of re-purposing a facility previously used for LNG to store liquified hydrogen or liquified ammonia is an interesting one. But is it feasible?
To store these gases safely, we need materials that can withstand cold temperatures and the chemical compounds they are in contact with.
While LNG is often stored in 9% nickel steel containers, the material is incompatible with ammonia due to the possibility of stress corrosion cracking. Nickel-alloyed carbon steel is also too brittle to be used below -200 °C – the temperature needed for storing hydrogen at ambient pressure. If the LNG containers are made of austenitic stainless steel, however, the chances of the facility being suitable for re-purposing for either liquified hydrogen or ammonia are higher. That is because some austenitic stainless steels can be used at cryogenic temperatures and most of them are sufficiently corrosion resistant when in contact with liquified ammonia.
However, the metals used to construct the tanks and pipes are not the only decisive factors for the success of such a project: the compatibility of all the valves, pumps, heat exchangers, and seals, among other things, must also be verified.
VTT – your knowledgeable partner in the hydrogen economy
VTT has a comprehensive understanding of materials and industrial processes. Leveraging our expertise, we can help you make the right material choices in the hydrogen economy. Through extensive testing and simulation, we help you find a suitable material that works in your application and the environment it is exposed to.
Want to find out more? Join our Tackling the material challenges in hydrogen economy webinar on November 23rd at 14:00 EEST. Leading VTT scientists will share their insight on:
- Material challenges related to the future of hydrogen and P2X processes
- How to transform process parameters and conditions
- Novel material solutions in new designs
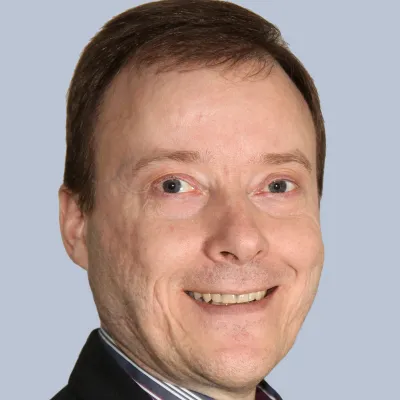